Unpacking the Tyre Industry: Value Chain & Key Raw Materials
Understanding the Backbone of Tyre Manufacturing
About the Tyre Industry:
The global tyre market was valued at USD 172.98 billion in 2024 and is projected to grow to USD 270.66 billion by 2033, with a CAGR of 4.70% from 2025 to 2033, according to IMARC Group. In India, the tyre market was valued at 202.17 million units in 2024 and is expected to reach 263.79 million units by 2033, with a CAGR of 2.85 per cent from 2025-2033. According to Anshuman Singhania, Chairman of the Automotive Tyre Manufacturers Association (ATMA), the Indian tyre industry is targeting exports exceeding $5 billion (Rs 41,655 crore) and aims to become one of the top three global tyre hubs by 2030.
The industry operates across three key segments—Original Equipment Manufacturer (OEM), replacement, and export markets—catering to a diverse range of vehicles, including two-wheelers, passenger cars, commercial vehicles, and off-the-road (OTR) vehicles. The OEM segment supplies tyres directly to vehicle manufacturers for new vehicles, while the replacement segment caters to aftermarket demand, providing tyres for vehicles already in use. The replacement market is the largest, contributing over two-thirds of industry volumes due to the recurring need for tyre replacements across all vehicle categories. The replacement market, contributing over two-thirds of industry volumes, is expected to remain stable due to strong demand across segments.
According to ICRA, tyre exports account for approximately 25 per cent of industry sales (by value). Indian-manufactured tyres are exported to more than 170 countries, with major markets like the EU, US, Brazil, UAE, and UK recognizing their quality. Exports currently stand at $3 billion (Rs 24,993 crore). With India's reliance on imported natural rubber, domestic NR prices play a crucial role in the industry's cost structure. Capacity utilization levels are estimated at 75-85 per cent in FY2024, with companies focusing on debottlenecking, process improvements, digitalization, and R&D for sustainable, high-quality tyre production. Additionally, rising environmental awareness and regulatory requirements are driving industry players to enter the tyre retreading segment, which ICRA expects to grow at a CAGR of 7-9 per cent during FY2023-FY2026.
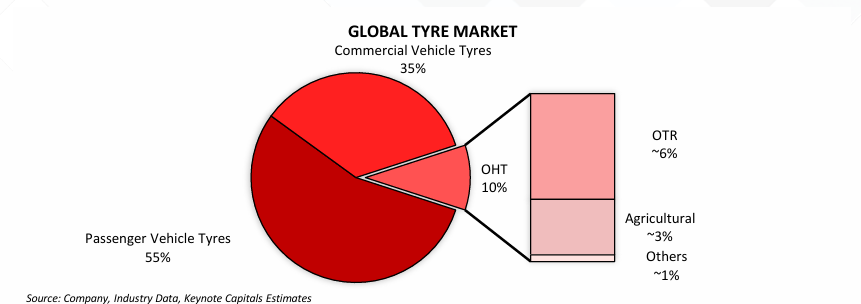
The tyre industry is a complex, multi-step process driven by a mix of natural and synthetic resources. Here’s a closer look at how tyres are made and the critical role petrochemicals play in their performance.
The Manufacturing Process:
The manufacturing of tyres typically takes about 24-36 hours from raw materials to the finished product. Here’s a breakdown of the time involved in each major stage:
- Mixing (4-6 hours): Raw materials like natural rubber, synthetic rubber, carbon black, and chemicals are blended to form the tyre compound.
- Extrusion & Component Preparation (6-8 hours): The compound is shaped into tyre parts (tread, sidewalls) through extrusion and calendaring.
- Tyre Building (1-2 hours): The green tyre is assembled by layering these components on a tyre-building drum.
- Curing (12-16 hours): The tyre is vulcanized in a press under high heat and pressure, giving it its final shape and durability.
- Finishing & Inspection (1-2 hours): Each tyre is tested for defects, balanced, and packaged for shipment.
Mass production in large-scale facilities allows manufacturers to produce thousands of tyres daily while maintaining quality and efficiency.
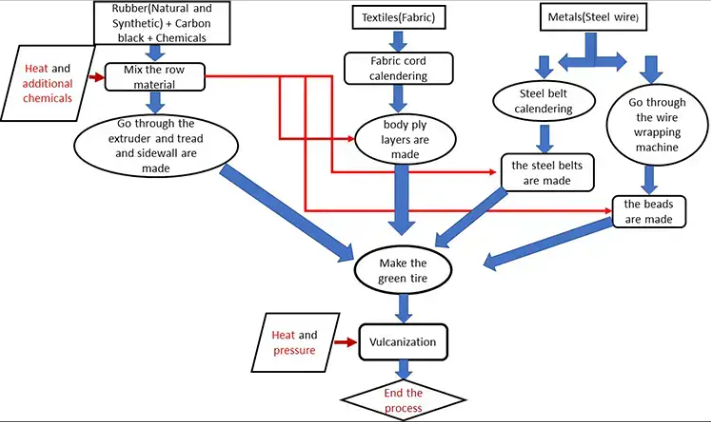
Key Raw Materials Driving Production:
- Natural Rubber (40-50 per cent of input): Sourced from plantations, providing elasticity.
- Synthetic Rubber: Primarily SBR (Styrene-Butadiene Rubber) and PBR (Polybutadiene Rubber).
- Carbon Black: Enhances strength and wear resistance.
- Steel: Used for bead wires and reinforcing belts in radial tyres.
- Chemicals & Additives: Sulfur for vulcanization, along with antioxidants and plasticizers.
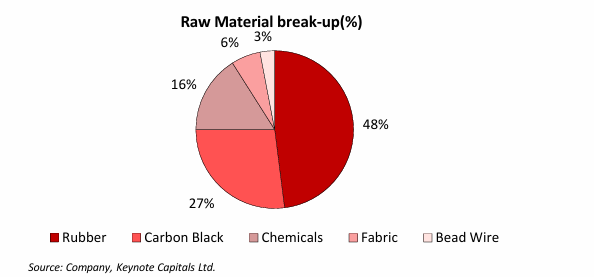
Raw Materials Sourcing:
Natural Rubber
- Sourcing: Mainly from Southeast Asia—Thailand, Indonesia, Malaysia, and Vietnam.
- Local Availability: Produced in Kerala and Tamil Nadu, but domestic supply often falls short, leading to significant imports.
Synthetic Rubber
- Sourcing: Derived from petroleum-based products, with major production hubs in the United States, Europe, and Asia.
- Local Availability: India has synthetic rubber manufacturing facilities, but still relies on imports to meet industry demand.
Carbon Black
- Sourcing: Produced from the incomplete combustion of heavy petroleum products, with manufacturing across North America, Europe, and Asia.
- Local Availability: India has a strong carbon black industry, led by companies like Phillips Carbon Black Limited and Birla Carbon.
Steel
- Sourcing: Sourced globally from major producers in China, Japan, and South Korea.
- Local Availability: India’s domestic steel industry meets a significant portion of the tyre sector’s needs.
Chemicals and Additives
- Sourcing: Sourced worldwide, including from Europe, North America, and Asia.
- Local Availability: India produces many chemicals domestically but imports specific additives for advanced quality and performance.
The Role of Petrochemicals in Tyre Performance:
- SBR (Styrene-Butadiene Rubber): A synthetic rubber made from styrene and butadiene—both by-products of petroleum refining. Improves traction and durability, commonly used in passenger car tyres (PCR).
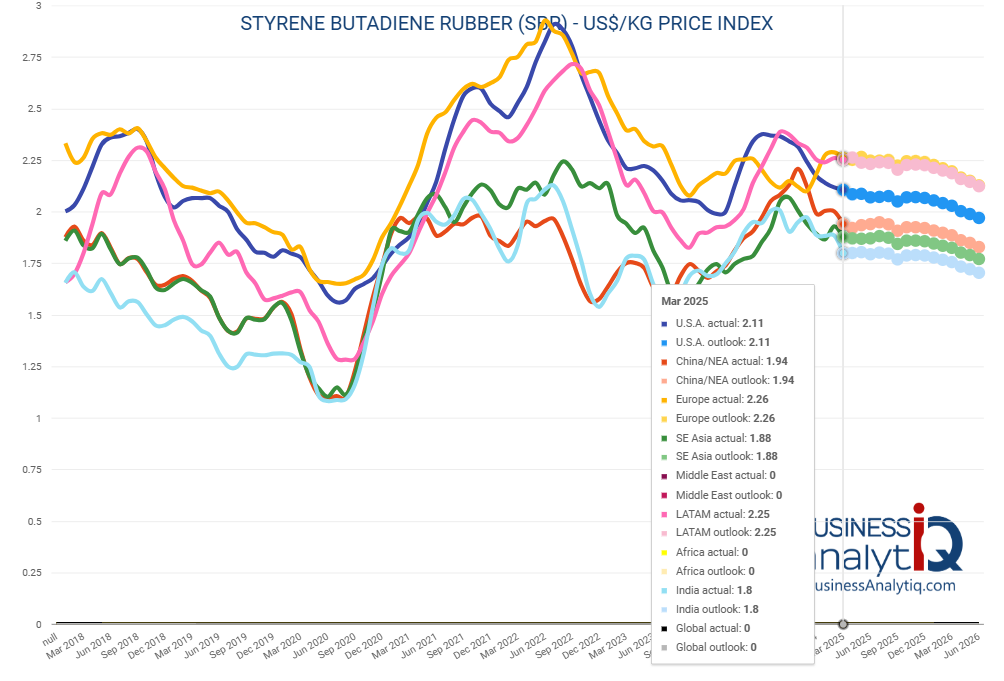
- PBR (Polybutadiene Rubber): A synthetic rubber made from butadiene, a petrochemical derived from crude oil. Essential for sidewalls, enhancing flexibility and crack resistance—critical for truck and bus radial (TBR) tyres.
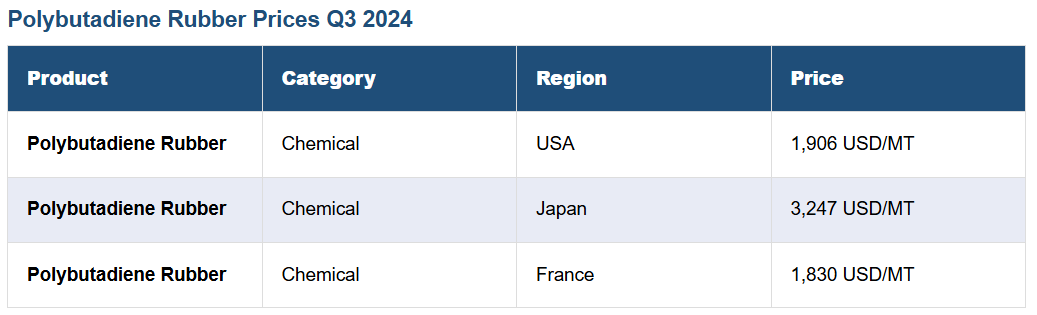
With increasing reliance on synthetic rubbers like SBR and PBR, the tyre industry remains closely tied to the petrochemical sector. As demand grows, innovation in materials and manufacturing continues to shape the future of mobility.
Disclaimer: The article is for informational purposes only and not investment advice.